この記事は、疲弊している製造業の品質保証部員に向けたものです。
過去記事でも述べていますが、製造業の「疲弊した品質保証部」から脱却するための参考になればと思っています。
攻めの品質保証部に転じるためのキーワードは「未然防止」です。
未然防止には色々な考え方や手法がありますが、どれが正しい手法かは分かりません。
ただ一つ言えることは、
未然防止の仕組みを社内に定着させ、「開発設計部門」、「製造部門」、「品質保証部門」が新たな製品やサービスを世に送り出す前にどれだけ設計やプロセスの信頼性について熟慮・議論をしたかが本質であると考えます。
もちろん「未来に起こる不具合を全て想定する」のは理想論ですが、熟慮・議論は時間に余裕さえあればできることです。
しかし、低コスト短納期で疲弊している企業には時間的余裕や人的余裕がない場合がほとんどでしょう。
その状況を打破せずに目の前の効率だけを追っていては、疲弊する体質は変わらず品質とともに人材も劣化していくことになります。
そういった企業を品質保証部が主導して立て直したい!
そういう方は、そのための知識習得や実践を通して自身の信念が確立されているはずです。
次にやることは他部門との意識合わせです。
こちらの主張を通すため、自らの信念を全面に押し出して相手を圧倒しなければなりません。
過去記事で、「ある場面での想定問答」を記載しています。
今回は、
開発部門に未然防止の取り組みに協力してもらうための想定問答
を考えてみたいと思います。
今回も主張を分かりやすくするため、あえて嫌われても仕方ないキツめのやりとりにしてますが、賢明なあなたはもっとスマートに対応できるでしょう(笑)
【vs開発部門管理職】「分かりきったことまで言わせるなよ!」って?どう考えたかの意図を見えるようにすることが重要なんですよ!
さて、不具合未然防止の手法としてはFMEAが有名ですね。
また、過去障害をデータベース化して設計時の参考とすることや品証部のチェックで使用するという手法もあります。
僕も、基本的にはFMEAが未然防止手法としては有効であると思っています。
しかし、FMEAシート作成に時間がかかることもあり、実際に実施する部門からは工数増の反発の声が上がるでしょう。
今回はこれに対する想定問答です。
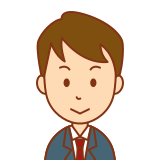
FMEAを活用した未然防止の仕組みを立ち上げたいと考えてます。
開発~量産プロセスの仕組み、FMEAシートのフォームや記入方法は品証部である程度作りこんだので、今度は開発部門の方で実践しながらフォームや仕組みの最適化していきたいんで協力をお願いします!
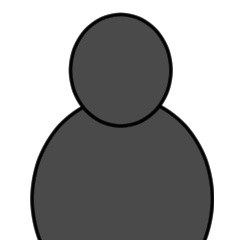
おいおい・・・
こんな「設計者では当たり前のような構造」の部分もFMEAの対象にするのかよ!
こんなのまでまともにやったら1日、2日じゃ終わらんぞ!
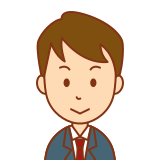
もちろん設計者の脳の中であらゆるリスクが想定されて対策が盛り込まれていれば、こんなことやる必要はないかもしれないでしょう。
でも、それがその特定の設計者だけの話であれば人によって設計品質のバラツキの原因となります。
だからリスクが少ない部分も、○○という理由があるからリスクが少ないという記録を残す必要があるんです。
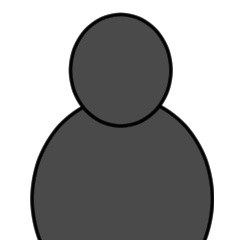
なぜそう思うんだよ?
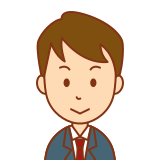
ベテランなどの熟練者が無意識でやっている「暗黙知」を誰でも分かる「形式知」にしたいんです。
そもそもあなた方は、今まで設計ガイドラインをまともに作ってこなかったから技術の継承ができず、担当が変わるごとに過去に起きた設計不良を繰り返してきてるじゃないですか!
図面の承認もほぼチェックもせずに「めくら印」でやってきたからこんな状況になってるんです。
当然僕らの監視も甘かったと思いますが、専門家でない分、品質の担保が不十分であったことは反省してるんですよ。
でも、お客様クレームから学んだ我々からのフィードバックが、次の新製品の設計に活かされていないのはあなた方の組織の問題ですよ!
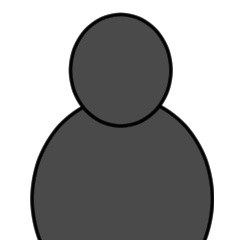
だったらお前らがレベルを上げりゃすむ話だろうが!
ウチの品証は技術的レベルが低すぎるんだよ!
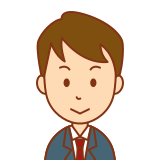
たしかに我々の技術的レベルはあなた方に比べれば低いです。
それが何か問題ですか?
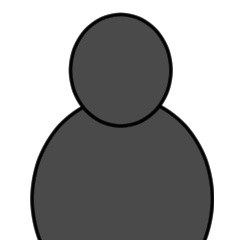
技術的な話が通じないのは「問題」だろうが!
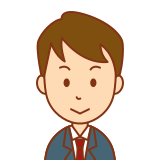
そりゃ技術的知見もあったに越したことは無いでしょう。
でも、品証部に本来必要なことは技術レベルを上げることですか?
我々の仕事は、あなた方の設計したモノが品質的に確かなものであることにお墨付きを与えることです。
技術レベルが低くても、あなた方が設計で作りこむ部分にどのようなリスクがあって、どのような対処をして、どのように評価したかが客観的数値になっていれば我々に「あなた方相当の技術レベル」が無くてもジャッジができるんですよ。
そういう仕組みを考えるのが仕事です。
そもそも我々にあなた方レベルの技術的知見があれば、あなた方の部門なんて必要ないじゃないですか!
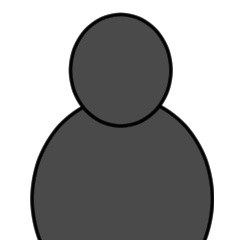
な、なんじゃとぉぉ~!
逆に聞くけど、お前らの言う通りにやって一体どんなメリットがあるっていうんだよ!すぐに効果が出るとは到底思えんけどな。
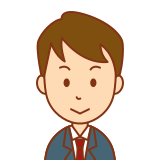
(まったく、どんだけ現状維持がしたいんだよ・・・やはり「本質の部分」は言わなきゃわからんか)
かけた時間分の金額的な効果は算出は困難でしょう。
でも、この活動で残ったドキュメントは設計ガイドラインになり得るし、我々も「あなた方の設計意図を容易に理解」することができる。
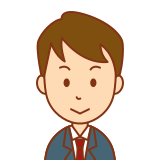
問題が起きなければ、このドキュメントを基に各設計者へのノウハウ継承資料になるので、世代間格差が大きいあなた方の部門で有用なはず。
問題が起きれば、そこは高リスクということで次回以降は同様の構造では対策を必須とすればいい。
また、問題が起きようと起きまいと設計時に議論を深めることで全員の品質意識を高めることができます。
この活動は継続と蓄積があって将来的に大きな効果を生むと確信しています。
対外的にも品質にこだわっているところをアピールできる証拠ともなります。
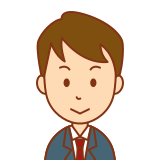
我々、「品質保証部」とあなた方「開発部門」、そして「製造部門」って今まで全然連携できてなかったじゃないですか・・・。
もうそんなの卒業して全社で意識を合わせないとメイド・イン・ジャパンブランドはどんどん海外新興国に抜かれてしまいますよ!
というかすでに中国にも抜かれてる分野もありますよ・・・
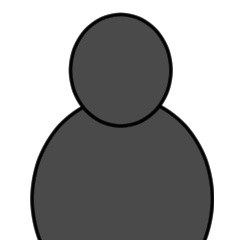
たしかに各部門で風通しは悪いよな・・・
でもいきなりそんなリソースは念出できんぞ!
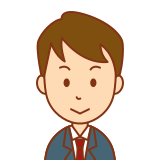
分かってます。
当面はこちらでたたき台を作成し、不足部分を追記修正してもらう形で我々主導で最適化を図ります。
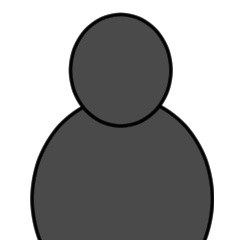
まあ、そこまでお膳立てしてくれてるなら試しにやってみるか・・・
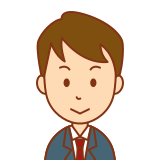
ありがとうございます!
なんかアツく語り過ぎてしまってすみません・・・
でも誰かが、なにか行動をおこさないと当面は現在のような状態のままで、将来を考えた活動ができません。
これが結果的に工程内とお客様先での不具合減少につながると信じて、
クレーム処理が減る
お客様からの信頼を取り戻す
ことに繋がると信じてやっていきます!
さいごに
というわけ、今回もハッピーエンドっぽく終わってますね。
説得する相手を圧倒すると言っても、論破して打ち負かすことが目的ではありません。
論破して相手のプライドをズタズタにして悦に入っているようでは、ただの自己満足です。
相手の立場を汲み、相手にこちらから歩み寄ることで仲間を増やしていかなければ、あなたの信念を具現化することができません。
自己満足で終わらせずに、結果を出さなきゃ意味がないんです。
現実は、
未然防止の活動は、やればやるほど時間がかかります。
効果もすぐには出てこないでしょう。
また事前に抽出されたリスクすべてに対策できない場合もあるでしょう。
でも一番大事なのは、
量産前にみんなでこんだけ真剣に考えたよ!
この記録を後世に残して役立ててもらおう
ということです。
この信念がなければ、せっかくの活動が形骸化して低パフォーマンスで終わってしまう可能性が高いのです。
最後に大事になってくるのは、従業員の品質に対する意識を高めることと、定着・展開を図ること。
これには地道な活動に加えて、経営トップからも先導してあげる必要があります!
トップダウンがいいとか、ボトムアップがいいとかどうでもいいんです。
ボトムとトップから挟み撃ちすれば早いでしょ?
現実は、簡単にはいかないでしょう。
それでも信念をもって粘り強くやってれば、仕事が楽しくなるはずです。
もしかしたら、個人単位ではそう思えただけでもハッピーなのかもしれませんね。。。
お互い切磋琢磨しましょう!
おわり
コメント