■この記事のターゲット
・製造業の品質保証部門
・製造業の工程設計者
・製造業の製造部門
今回の記事では、製造業の品質保証部門の立場として「信頼性の高い工程設計」を考えてみたいと思います。
何事も最初が肝心!
信頼性の高い工程とは、要求された付加価値を要求の範囲内で繰り返し再現できる工程であると考えます。
最初の設計にしっかり時間をかけて、「質の高い工程」を生み出すことで後々のトラブルが減ります。
どこまで考えたかによって、その工程の行く末が決まると言っても過言ではないのです。
FMEAなどのトラブル未然防止ツールは、設計された作業に対して行われるものです。
設計されていない項目に対してはリスク抽出ができないので、どこまで細かくポイントを抑えた設計ができるかで工程の信頼性が決まります。
しかし、時間をかけ過ぎて機を逸することがあってもいけません。
また、なんでもかんでも細かく設計しすぎて工程の自由度(現場の裁量)を無くすと、現場内の改善で生産効率を高めることができなくなります。
製造業で20年以上エンジニアとして、品質保証部門として働いてきた経験を基に
「どういう観点で、どのような項目を検討すればいいのか?」
について述べていきます。
筆者の経験から、考えておきたい項目を以下の表に示します。
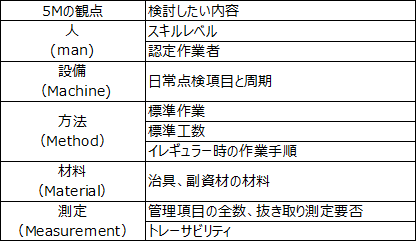
何かを設計するときは、一つ一つの作業や工程を5M(Man、Machine、Method、Material、Measurement)の観点で整理して考えると設計漏れが少なくなります。
ビジネスの基本要素QCDES(Quality、Cost、Delivery、Environment、Safety)は、5Mで成り立っているからです。
それでは5Mの観点でもう少し具体的に設計検討項目を掘り下げていきます。
工程設計における「人(Man)」について
最も工程の信頼性を左右する項目と言ってもいいかもしれません。
なぜなら、「人はミスする生き物」だから。
正直言って、人に対してどこまで設計で入り込めるかは難しいです。
人の不完全性というリスクを排除するにはロボットやAIなどを活用するしかありません。
しかし、資金が潤沢な企業でなければ大きな投資は難しいところでしょう。
もちろん、ロボットやAIを設計・導入するのも人間なので、機械化したから大丈夫というのは思考停止状態です。
ロボットやAIの設計、導入の工程をしっかり設計しないといけないことに変わりはありません。
話は逸れましたが、「人」について最低限考えておきたい項目を述べておきます。
その工程で作業する人のスキルレベルはどの程度を要求するのか
ある工程で作業する人は、入社1年目の人間でいいのか?
それとも、同様の作業を3年以上の経験したベテランがやるべきなのか?
ある工程で作業できる人間を限定することは、製造現場の人員やりくりが困難になるので望ましくありません。
しかし、誰がやってもいい工程とそうでない工程が存在してしまうのが現実です。
例えば検査工程。
ある程度教育されたとはいえ、入社2か月目の人が量産工程の最終試験を行うのには大きなリスクが伴います。
人を限定する場合は、製造現場のルールにするか工程設計でドキュメントに明記してあいまいにしないようにしましょう。
例えば、以下のように限定します。
例)類似作業の経験が1年以上の者
例)類似作業の経験が1年以上の者が一定期間作業指導した者
大した内容ではないですが、設計者の意図として「この工程は重要だよ!ちゃんと考えたよ!」ということを自他共に知らしめることができます。
設計者の意図を他人に分かってもらうことが重要なのです。
第三者がドキュメントを見ただけで設計者の意図を読み取れるということは、設計者の想いを他人が再現しやすくなるということです。
その工程は、社内で認定された者のみが行える作業とするか
前述のスキルレベルと似たような話ですが、認定作業者の制度がある会社では工程設計者は設計しやすいですね。
会社として、こういう作業には「資格が必要」としているので、工程設計者は有資格者を対象の工程に当てはめればいいだけです。
このような制度がなければ、新たに設置することをおすすめします。
例)〇ヶ月以上の実務を経験し、筆記と実技試験をパスした者に資格を与える。
別にどこの部門がルールを作ってもいいと思います。
工程の作業品質を高めるための全社的なルールなので、品証部門だろうが製造部門だろうがどちらでもよいのです。
特に技能を要する作業(経験とセンス)は資格者制度としたほうが、前述の抽象的なスキルレベルよりも曖昧さは減ります。
曖昧な部分が減るということは、品質にばらつきがでにくいということです。
「人による作業」については5Mの「方法(Method)」の項で述べます。
工程設計における「設備(Machine)」について
多くの企業では、製造技術や生産技術部門といった量産を技術的に支援する部門があります。
加工設備の導入や条件設定などをすることになりますが、製造工程の設計者は生産技術部門が導入した設備の日常点検項目を確認しておく必要があります。
当たり前ですが、設備が放置でいいわけがありません。
設備トラブルや消耗による加工精度の悪化など、設備保全不備で起こるトラブルも多いのです。
・どのような保全計画なのか?
・現場の作業者に日常点検させるのか?させるなら内容と周期は?その内容と周期でいい根拠は?
製造現場が設備によるトラブルで困らないようにしっかりと確認しましょう。
製造現場で日常点検をさせるなら、それは製造工程の作業の一部です。点検内容と周期、点検結果の記録までを手順とし、日々の確認漏れがないようにする設計が求められます。
ルーチン作業に加えて点検に必要な工数も入れ込んだうえで設計しないと、
「余裕ないからできませんでした・・・」
みたいな言い訳が飛んできてしまいます。
設計者の意図として、「日常点検も重要な作業のひとつだよ」と表明しておきましょう。
もちろん検査設備も重要です。
最近は外観検査をカメラと画像診断で行う企業も増えています。
技術部門と品質保証部門の仕事の範疇かと思いますが、工程設計者としても設備の精度を確認しておきましょう。
・正解データ、NGデータの登録は終わっているか?
・虚報は何%で設定しているか?
・現場の作業者にやらせることはあるか?
画像診断に頼り過ぎた場合、最初の診断精度が悪いと不良品流出につながります。
しっかり確認して、目視外観検査が必要なのか、必要な場合はどのレベルの人を充てればいいのか検討しましょう。
工程設計における「方法(Method)」について
人が行う作業の設計も最も重要な項目のひとつです。
どれだけ付加価値を生む要素作業(○○を取る、○○を○○に差し込むetc…)を列挙しましょう。
・その作業ごとに明確な作業指示、注意喚起をしているか
・決めた作業手順を高確率で守れる仕掛けを入れるか
・決めた作業をしなかった時に生じる不具合を後の工程で気づける仕掛けを入れるか
ここは工程設計者の腕の見せ所です!
その工程で必要な作業は何なのか(標準作業の設定)
あるひとつの工程の中で、要求する付加価値を生み出すために複数の要素作業が存在します。
要素作業を順に列挙したら、
・加工、手順を間違えないようにどこまで細かく指示しているか
・加工を終えた後に、正しく加工が終わっているか見る必要があるのかないのか
・正確な作業を人任せにするのか、治具を使うのか
作業する人の立場になって、極力曖昧さがない指示をすることでバラツキの少ない成果物ができあがります。
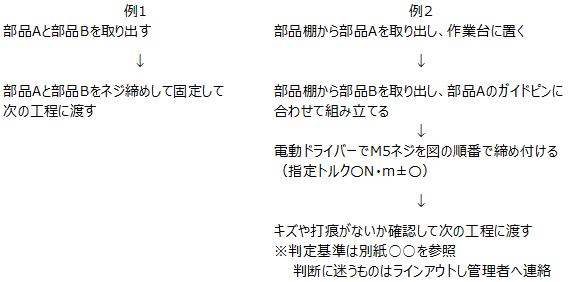
さらに工程の信頼性を高めるために、決めた作業手順を意識しないでも守れるように、守らなかった時は次の作業に移れないようにといったヒューマンエラー防止策を入れ込みます(いわゆるポカヨケ)。
設計の段階で工程の信頼性を高めるにはFMEA(故障モード影響度解析)が有効です。
工程FMEAについては、別の記事に詳細を記載していますので参照ください。
FMEAを効果的に行うためにも品質面で重要な要素作業は指示内容を明確にする必要があります。
リスク抽出する対象作業が明記(設計)されていなければ、リスク検討すらできないからです。
標準作業工数も設計しよう
標準作業が決定したら、作業に要する工数を見積もることになると思います。
「この作業に何秒かかるか?」という観点だけではなく、
「この作業を確実に行うためには〇秒必要だ」という観点も必要です。
確実性が求められ、失敗しても後で検出できず市場影響が大きい付加価値作業では慎重な作業が必要です。
何度も繰り返し作業する場合は、疲労や集中力の限度をある程度加味してあげないとヒューマンエラーが起きやすくなります。
人の力を借りずに機械やコンピュータを活用できればいいですが、そうもいかないものは安定した作業ができる時間を確保すべきです。
例えば、ワイングラスを割ることなく5段積みするとしましょう。
「30秒でやれ」という場合と「10秒でやれ」というのはどちらがガラスを割る可能性が低いでしょうか?
もちろん30秒ですよね?
そうじゃない!という人は、10秒で100回繰り返しても1回も崩さずにできる自信がある人なんでしょう。
言いたいことは、誰が繰り返し作業をしても安定して作業ができる時間を用意してあげようということです。
当然、時間を取り過ぎると生産能力は落ちますが、品質を落とさないことを前提に改善を進めていくのが筋というものです。
不良を出すリスクがあるまま、スピードだけを速くしてもいいことはありません。
まず最初にリスク度合いに合わせた工数の設定をして、工程の習熟と機械やからくりのチカラを活用してスピードを上げていくのが理想です。
要は根拠のあるスピード設定をしてあげましょうということですね。
もちろんスピード設定したら、設定よりも遅くても速くてもいけません。設定の通り作業することで設計した工程を再現できるのですから。
なので、スピードを上げるということは設計変更(4M変更)です。
イレギュラーが起きたときの手順も設計してますか?
不具合が起きるときの多くは、イレギュラーな状態になった時です。
例えば、
・設備のトラブルが発生したので仮の処置をして流した
・普段一人で作業するところを二人で作業した
・作業の遅れがでたから応援に入った
などが挙げられますね。
想定されるイレギュラーが発生した時は、復旧させる時の手順やイレギュラー対応時のルールなどを決めておく必要があります。
多くの企業ではそこが不明確であり、場当たり的な対応をするから不具合が発生するし、再発してしまうのです。
イレギュラーをすべて想定することは困難かもしれません。
少なくとも想定されたイレギュラー対応手順が守れるような工程設計をすると、FMEAで信頼性評価ができるので工程の信頼性が大きく向上します。
可能な限りイレギュラー対応を想定しましょう!
工程設計における「材料(Material)」について
工程設計での「材料(材料)」の観点ってなんでしょうかね?
何に当てはめるのが適切なのか意見が分かれるところですが、それなりに熟慮して出した答えなら何と解釈しもいいんじゃないでしょうか?
使用する治具の材質
消耗品の材質
治具の材質
というような分かりやすいものに解釈してもいいでしょう。
ここでは、一般的に使用する副資材(工程内で使用する緩衝材やテープなど)を考えてみたいと思います。
副資材となると工程設計部門が決めるものではないかもしれません。実際には現場の裁量で変えているものもあるでしょう。
可能であれば、この副資材も指定されたものを使うように指示するのが望ましいです。
変化あるところに不具合発生リスクありです。
技術的な見解や採用可否は技術部門や品証部門に任せるとして、何をどうやって使うかを意図をもって決めておくことは重要です。
意図や目的が共有されてないと、人が入れ替わった時などに何も考えずに現状を変更される可能性があります。
工程設計における「測定(Measurement)」について
ここでいう測定には2種類あります。
ひとつは、要求される品質のウォッチです。
加工した製品の寸法や重量など定量的に測定し、要求仕様に対する合否判定、または数値の推移をみて未然防止の活動に役立てるためのもの。
もうひとつは、トレーサビリティのための記録です。
これはトラブルが起こった後に原因を調べるために必要な記録になります。
何時何分に、どこの工程を通って、誰が作業したかなどですね。
どちらも重要な測定内容なので会社としてのルール、または技術部門や品証部門から指示があることが殆どであると思います。
当然工程に組み込まれるからには、測定の要素作業の信頼性も高めなければいけません。
全数測定なのか、抜き取り測定でいいのか、測定する項目と工程の作り込みでどれだけ保証できるかを考慮して、品質保証部とも連携しながら設定するとトラブル未然防止、トラブル発生時の早期原因究明に役立つことは間違いありません。
データをどれだけ集めることができて、どれだけ速く意思決定できるかが未然防止にもトラブル解決にも重要であるということです。
まとめ
再度、工程設計の際に考えておきたい項目を以下の表に示します。
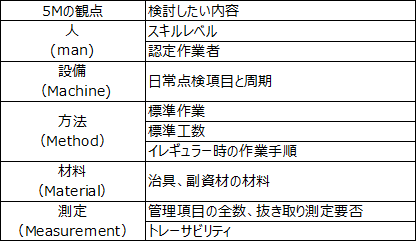
くどいようですが、最初の設計でどれだけ考えて想定されるトラブルに対して設計側で予防策を入れ込んだかが工程の信頼性を左右します。
作業者、オペレーターのせいにしてはいけません。
トラブルの原因は上流での設計に問題があるからです。
しかし、全てのトラブル想定ができず、問題が発生しても落ち込む必要はありません。
次の設計に活かす糧にすればいいだけですから。
一歩ずつ進めば、いつか自分の納得できる設計ができると信じて精進しましょう!
おわり
コメント