■この記事のターゲット
製造業の工場で業務に従事していて、
・静電気対策は最低限何をやっておけばいいの?
・静電気で部品が壊れるけど、どう対処すればいいの?
・静電気対策をやれば静電気破壊は確実にゼロになるの?
という疑問を持っている持っている方。
過去から、電子部品や電子機器を製造する工場を悩ませる静電気によるトラブル。
扱う材料や製造方法で様々な静電気発生要因があるため、原因調査にも時間がかかるし、効果が確実に読めないこともあり積極的に投資するのも判断に迷います。
今回の記事では、これまで複数社にわたり製造工場のエンジニアとして勤務してきた中で、工場内の数々の静電気問題に向き合い、静電気破壊のメカニズムと対策を学んできた筆者の経験から「基本的な静電気対策」を述べてみたいと思います。
この記事が、あなたの現場での静電気対策に少しでもお役に立てれば幸いです。
早速ですが、静電気の基本的な対策を以下に挙げます。
・帯電しているものを持ち込まない、持ち込ませない
・重ねたり擦ったりして物体を帯電させない
・帯電した場合は速やかに除電する
帯電:物体が静電気電荷を帯びること
物体がプラスの電荷、またはマイナスの電荷過多となり、基準電位に対して電位差を持つ状態になること。(通常はプラスとマイナスの電荷は均等に釣り合って電位差が発生していない)
おおよその静電気トラブルは上記の対応で解決ができると考えます。
しかし、静電気を発生させる要因は数多く存在するので、多くの要因から対応すべき対象にピンポイントでフォーカスできるかどうかが問題になってくるのです。
当然ながら静電気は目に見えないこともあり、現実的にはトライアンドエラーを繰り返して抽出したリスクを一つ一つ潰していくしかありません。
(テクノロジーを駆使して可視化できる手段も出てきています)
考えうるすべての要因を潰しこんでも静電気トラブルをゼロにすることは困難かもしれませんが、リスクを減らすことが静電気破壊の確率を下げることは間違いありません。
静電気発生のメカニズムや具体的なトラブル事例は別記事で詳細を述べるとして、今回は「リスクを潰しこんでいく観点を知るため」という点で静電気対策の基本について述べたいと思います。
静電気問題のトレンド
まず事前に知っておくべきことですが、一般的に世の中の電子部品は静電気に対して耐力が弱くなっていくトレンドです。
なお静電気耐力を説明すると、
・静電気電荷放電の瞬間的な大電流による局所熱ストレスで回路が溶断
・帯電による大きな電界下(電圧)による絶縁破壊
などの現象への耐性と言っていいでしょう。
その耐性低下のトレンドの要因としては、コストダウンが挙げられます。
従来の電子部品やそれらを組み込む電子回路には、静電気放電による電気的ストレス(大電圧や大電流)の耐力を持たせるような設計であった、もしくは意図せずとも一定以上の耐力をもつ構造であったと言われています。
しかし競争が激しい分野などでは価格競争のため、メーカー側は過剰な実力を持たせずに実使用上問題ないであろうとされるレベルまで静電気耐力を下げて、フィルター機能を削除するなどでコストダウンを行っています。
さらにもう一つの要因として挙げられるのが、部品の高密度化・高機能化です。
ICの開発の世界では、ダウンサイジングによる内部回路の微細化、複数の機能を1つのパッケージで実現するための高機能化による内部の高密度化(=微細化)が年を追うごとに進んでいます。
これにより、内部導体配線は細くなる、隣接するパターン間距離が短くなるなどで静電気放電耐力の実力値は下がっている傾向です。
よって、これまではある程度「雑な」静電気対策管理でも顕在化することが無かった静電気トラブルが、近年多くの工場で顕在化してきているのです。
静電気対策の基本「3原則」
冒頭に挙げた静電気対策の基本3つについて、詳しく述べたいと思います。
一般的な電子部品や電子機器の工場では、当たり前として認識されている部分があると思いますが、静電気発生要因は数存在するために見落としがちになるということも現実として起こっています。
まず確認すべきポイントの前に、対策の基本を確認しておきましょう。
帯電しているものを持ち込まない・持ち込ませない
帯電しているものを持ち込まない(持ち込ませない)とありますが、帯電するものは無数に存在しています。
そんな中で、一般的に工場で多くみられる帯電物は「部品」や「副資材」ですね。
当然設備や作業机などもそうですが、一般的な電子機器工場であれば後で述べる工場アースへの接続により「等電位結合」で電荷が貯まらないように、または静電気電荷が発生しても工場アース側へ逃がすことで電荷が貯まらないようになっているはずです。
工場外部から持ち込まれる「部品」や「副資材」は、帯電防止の包装をしていない限りは、輸送の振動などによる物体と物体の接触や摩擦により静電気が発生します。
特に樹脂やゴムなどの絶縁物は、静電気電荷が貯まって(帯電して)も絶縁物であるがゆえに貯まった電荷が移動しにくいので、後で述べる工場アースへの接続で意図的に放電させるのが困難です。
帯電している樹脂カバーなどは、その単体が電子部品に触れて破壊させるエネルギーは比較的小さいですが、工場アースに接続されていない金属などの導電体に近接させると導電体を帯電させてしまいます(誘導体電)。
帯電した金属などの導電体は、静電気電荷が放電するときのエネルギーが大きい(電流が大きい)ため電子部品の破壊リスクが大きくなります。
よって、絶縁物は電子部品を取り扱うエリア(静電気管理エリア)には極力持ち込まないほうが良いのです。
なお絶縁物は導伝物よりも非常に抵抗が高いため、工場アースに接続しても電荷がほとんど移動せず、速やかな除電は望めません。
それでも持ち込まないといけない場合もあるので、のちに触れる「イオナイザー」という徐電器で電荷の偏りを中和する(=除電)という方法がしばしば取られます。
ですが、イオナイザーや工場アースへの接続で除電したものを「静電気管理エリア」に持ち込んだ後も帯電する可能性があることを忘れてはいけません。
物体同士を重ねたり擦ったりして物体を帯電させない
静電気が発生する原因としては、主に以下のようなものがあります。
①物体と物体の接触(物体間の摩擦、剥離も含む)
固体同士はもちろん、固体ー液体、固体ー気体など物体の状態にかかわらず、接触で発生する。
②帯電物の近接による誘導体電
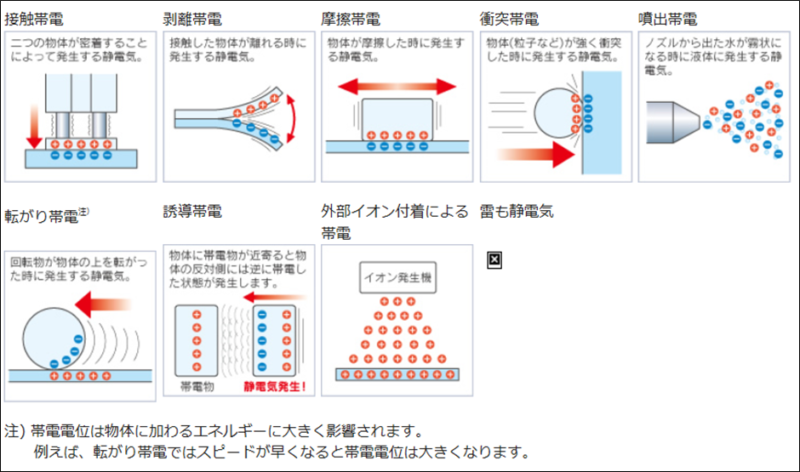
それぞれの詳しい説明は別記事で述べたいと思いますが、簡単に言うと
①:物体固有の性質により物体同士が接触、または接触⇒剥離や摩擦を行うと、その固有の性質により静電気電荷の偏り(プラスの電荷過多またはマイナスの電荷過多)が発生するというものです。
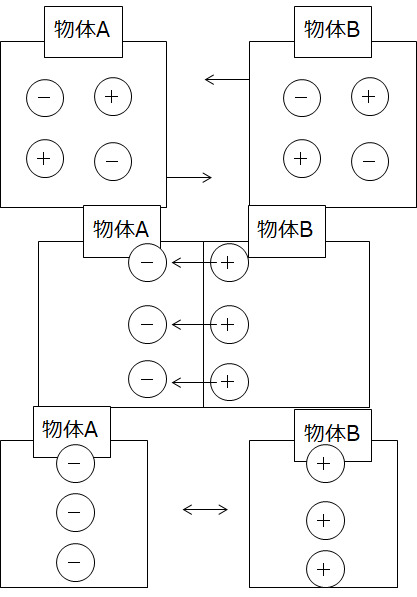
②:静電気電荷を帯びた(帯電した)物体が電気的に中性な物体に近づくと、プラスとマイナスの電荷が引き合う「クーロン力」によって引っ張られ、電荷が物体内で偏ることで見かけ上、帯電しているように見える現象です。
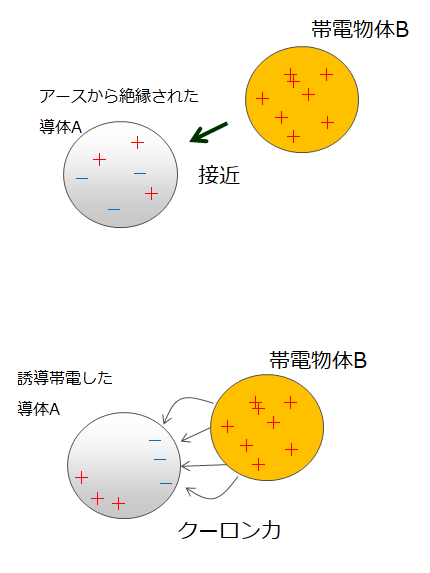
前項のように、帯電していない物体をEPA内に持ち込んでも、その後の取り扱いによって帯電させてしまう可能性は十分にあるのです。
例えば上記①、②の例で考えると、以下のような状況が想定できます。
・樹脂板のような絶縁物を平坦な作業台に置いて、持ち上げた ⇒ これだけで静電気が発生します。
・その帯電した物体をアース接続されていない金属に近づけた ⇒ 金属が誘導体電で帯電する
よって、作業台の形状変更(接触面積を極力減らす)やアース接続を行うなどの対応が必要となり、それらを維持管理しないといけないのです。
帯電した物体は速やかに除電する
前項で述べたように、物体は簡単に帯電(静電気電荷を帯びる)します。
よって、帯電した物体を速やかに電気的に中性(プラスとマイナスの電荷の数と分布が均等な状態)にしなければなりません。
その基本的な対応として「工場アースへの接続」があるのです。
電子機器を扱う工場では一般的だと思いますが、
・作業台や設備をアースに接続する
・人体をリストストラップ(アースバンドとも呼ばれる)や静電気防止靴と導電床を介してアースに接続する
などが行われていると思います。
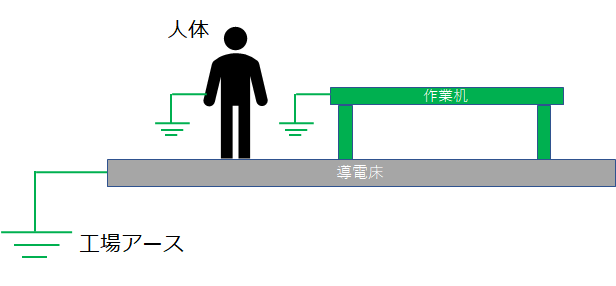
アース接続が「簡単かつ最善の除電対策」と言っていいでしょう。
ただし、これは金属などの「導体(体積抵抗率が低い物体)」に限った話であり、電気伝導が限りなく小さい樹脂や紙などの「不導体(体積抵抗率が極めて高い物体)」ではアース接続による静電気電荷の移動はほとんど見込めません。
そのような「不導体」の除電には、後述する「イオナイザー」という除電アイテムが有効であることが知られています。
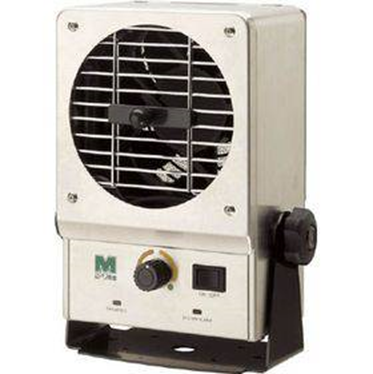
卓上ブロワータイプ
静電気の問題が起きた時に「まず確認すべき」ポイント
電子部品を扱う一般的な工場は、過去からある程度の静電気対策が実施されていると思います。
それでも静電気トラブルが発生してしまう要因は、大きく分けて2種類に分類されると考えます。
・本来遵守すべきルールを守れていない=管理監督、従業員の静電気対策への意識の問題
・静電気発生リスク箇所を理解しておらず、対策しきれていない=知識や経験の蓄積が不十分
静電気要因が疑われるトラブル(主に電子部品破壊)が起きた時にまず疑うべきポイントは、上記観点を持ったうえで前項で述べた「3原則」の裏返しから抽出するのが王道と思っています。
帯電しているものを持ち込んでいるか?
帯電しやすい部品や副資材(特に樹脂系の物体)が無いかを確認します。
帯電量の測定は、一般的に表面電位計で測定が可能です。
作業台に置いた状態だけでなく、組立や加工で使われる状況での帯電量も確認しましょう。
このとき、工場アースに接続された作業台上に置かれた物体と、そこからその物体を持ち上げた場合とで帯電量が変わるので注意が必要です。
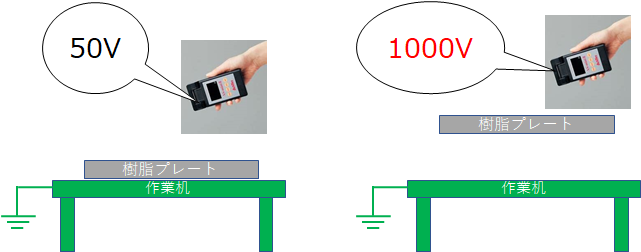
これは、剥離帯電の可能性もありますが、「容量効果」と呼ばれる電極間の距離の変動に伴う静電容量の変化と電圧の変化も関係してきます。
※詳細は別記事で述べたいと思いますので、ここではイメージのみ説明します。
静電気の基本式:Q=CV Q:静電気電荷、C:静電容量、V:電位
物体の電荷量は変わらないので、アースなどとの距離で静電容量が変化すると、上記式の関係でQの値を維持するようにVも変化するというもの。
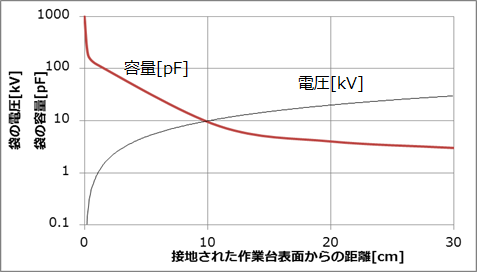
そもそも持ち込んではいけないものを管理エリアに入れてしまっている問題なのか、管理された状態で管理エリアに入れたあとに帯電してしまった問題なのかを切り分ける必要があります。
参考:帯電量の管理値目安の設定と人体モデル、マシンモデル
なお物体の帯電量をどのくらいで管理すべきかというと、
RCJ(日本電子部品信頼性センター)の規格RCJS5-1では、HBM(Human Body Model:人体放電モデル)100V以上の静電気敏感デバイスを扱うための規格が謡われているので、まずは100Vが一つの目安となるでしょう。
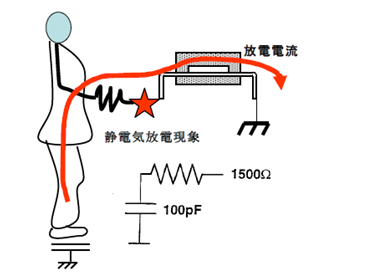
もちろんこれは絶対に守らないといけないというわけではありません。
一般的に広く使われる電子部品のデータシートでスペックを確認すると、HBM1000V以上というような記載があります。
部品単体では、人体経由での静電気放電で1000V以上の実力値を持っているという事になります。
使用する電子部品により、どのレベルで帯電量を管理するか参考とする必要があります。
モノによってはHBM50V以上というデバイスも存在するので、実際に破壊されているデバイスによっても目安となる管理値は変えていく必要があるでしょう。
ちなみにデータシートにはMM(Machine Model:マシン放電モデル)○○Vという記載も見られます。
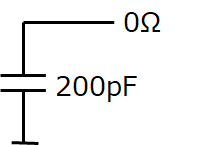
MMは設備や工具などの金属とデバイスの放電を想定した放電モデルです。
金属は人体よりも抵抗値が低く、さらにアース間の容量が大きいため、ひとたび静電気放電が起こると大きな電流が流れます。
よって人体モデルよりも低い静電気帯電量でデバイスを破壊させてしまう可能性があるので最も注意しておく必要があります。
これまでの僕の経験と、講習会などでの講師へのヒアリング結果から、おおよその静電気トラブル(部品破壊)の主な要因はマシンモデルによる放電であると思っています。
設備や治具の金属部分が、工場アースに対して絶縁されているような場合だと、なんらかの理由で摩擦や誘導体電を起こし、デバイスを破壊させるリスクになるというものです。
(例:金属治具の摺動部が絶縁されていたなど)
普通の管理がされている工場であれば、人体は電気を通しやすい静電気対策靴⇒導電床⇒工場アースという経路でアース接続されています。
立ち作業をする限りでは、飛んだり跳ねたり走ったりしても人体の静電気電荷は靴⇒床⇒工場アースという経路で等電位結合され、人体の表面電位はおおよそ50V以下程度にしかならないことは実験的に分かっています。
言いたいことは、リストストラップを着用する場合も含め、靴や導電床の抵抗値日常チェックが問題なければ、人体からの静電気破壊というのは要因として除外しやすいということです。
それよりもMMモデルの放電リスクがないか(金属の数百V以上の帯電)に絞った方が、原因に行きつく可能性が高ると考えます(あくまで経験上ですが)。
物体同士を重ねたり擦ったりして物体を帯電させる要素があるか?
前述したように、物体を重ねる⇒剥離させる、物体同士を擦るという行為は「静電気発生のリスク」を高めます。
とくに平坦な樹脂製フィルムや板などは、接触面積も広いため大きな静電気電荷が蓄えられやすくなります。
樹脂自体は導電体ではないので、ICなどが直接触れても大電流が流れ込むリスクは低いですが、問題は帯電した樹脂が工場アースに接続されていない金属に近接したときに、誘導体電により金属を帯電させてしまうリスクの方をとらえるべきです。
元となる樹脂を帯電させないようにするか、金属側を工場アースに接続するなど状況に合ったアプローチを選択する必要があります。
帯電した物体は速やかに除電できてる?
順番的には最初に確認すべき項目かもしれません。
一般的な静電気対策といえば、人体・作業台など電子部品に直接触れる恐れがある物体(特に導電体)のアース接続です。
基本的には数Mオーム~数百Mオームの抵抗を介してアースに接続されているはずですが、もし接続されていない物体があると、それは静電気的に大きなリスクになり得ます。
なお、アース間にある程度の抵抗値を持たせる意味は、静電気電荷の放電による電流の最大値を抵抗で抑えるためです。
もし0オームに近い形でアース接続していると、帯電したICが触れた時に大きな電流が流れてしまうからです。
導電体の除電の基本はアース接続(等電位結合)ですので、静電気対策管理している靴や作業台、治具や設備が確実に(既定の抵抗値を持って)アース接続されているかを確認しましょう。
除電のためのイオナイザーや局所ミスト装置ってどうなの?
静電気対策の基本は、すでに述べた「3原則」であり、除電の基本はアースへの接続による等電位結合です。
しかし、絶縁物の除電はアース接続では効果がほとんど見込めないため、追加対応としてイオナイザーによる静電気電荷の中和という手があります。
イオナイザーにより、プラス電荷またはマイナス電荷を生成⇒放出し、帯電物表面が電気的に中性になるようにさせる設備です。
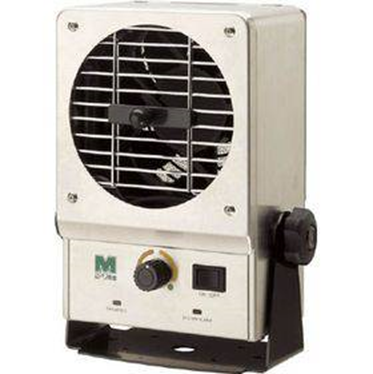
卓上ブロワータイプ
イオナイザー内部の電極針先端に高電圧を印可し、コロナ放電を発生
↓
コロナ放電により、周囲の空気にプラスイオンとマイナスイオンが発生(電離現象)
↓
送風または帯電物とイオンが引き合う「クーロン力」によって、帯電物表面の電荷が中世になるようにするメカニズム
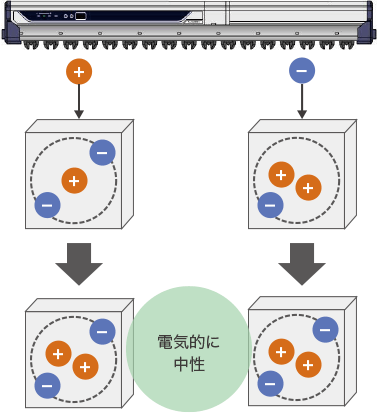
キーエンスHPより引用
設備の日常管理が必要になりますが、正しく使用すると大きな除電効果を生むので、アース接続で対応できないケースでは有効な手段のひとつと言えます。
また、局所ミスト装置を使用する手もありますが、個人的には推奨しません。
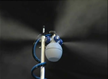
たしかに周囲の湿度を一時的に上げることによって、空気中の水分を利用して帯電物表面の静電気電荷が中和するスピードを速めることで帯電量を下げることができます。
しかし、使用する水のコスト、水による周囲の部品の結露や腐食、腐食を嫌って純水を使用すると水の抵抗値が高くなるので噴霧時に逆に静電気を発生させるおそれがあります。
僕は過去に局所ミストを使用している工場で、はんだ付け不具合が多発した経験もあるので個人的には導入否定派です。
まとめ
今回の記事では、静電気対策の基本は以下の3つということを述べました。
・帯電しているものを持ち込まない、持ち込ませない
アース接続できない金属や不要な絶縁物は極力持ち込まない管理体制づくりなど
・重ねたり擦ったりして物体を帯電させない
モノを不必要に重ねたり擦ったりさせないルールの浸透、作業台との接触面積を減らす工夫
・帯電した場合は速やかに除電する
帯電した場合は速やかに除電する。 人体を含む導電体のアース接続(等電位結合)の実施と維持管理。
帯電しやすく、除電が困難な樹脂などの絶縁体は、イオナイザーを活用して除電する。
また、静電気トラブルが起きたときにまず確認すべきポイントについても述べました。
・静電気対策のための靴、作業台などのアース接続状態(抵抗値で測定)が管理値内かどうか
・特にうすっぺらい樹脂や、アースされてない金属の帯電量を確認
・作業台に置いてある状態と作業中の状態それぞれでの帯電量を確認
静電気トラブルの調査と対策はトライアンドエラーの繰り返しでリスクをつぶしていく。
静電気トラブルの調査と対策はトライアンドエラーの繰り返しでリスクをつぶしていくのが基本です。
基本を守れば、おおよその静電気トラブルは防げるが、発生源と放電のメカニズムを解明するのが骨が折れるところ。
投資に対する効果が見えにくいので、静電気対策に対する会社の方針を明確にする必要がある。
今後、静電気のトラブル事例や発生のメカニズムにも触れていきたいと思います。
おわり
コメント