■この記事のターゲット
・FMEAの本質を理解したい
・FMEAを使って全社的に未然防止にチカラを入れたい
・FMEAをすることでどんな「メリット」があるのか知りたい
今回の記事は、過去記事でも何度か触れてきたFMEA(故障モード影響度解析)についてです。
過去記事では製造業での工程FMEA(P-FMEA)を例にして、FMEAの本質は「設計の信頼性を数値化して残すこと」としました。
設計した製品やプロセスの「不具合未然防止」にはFMEAしたほうが良いのは分かるけど、具体的にどんなメリットがあるのでしょうか。
メリットがあるのは設計部門だけの話なのでしょうか?
品証部門だけの話なのでしょうか?
答えはNo
FMEAを全社一丸となって実施し、そこで得られた結果に基づいて行動する組織力があれば、会社全体にメリットをもたらすことも可能なんです。
これは製造業に限った話ではありません。
すべてのビジネスにおいては「設計」というものはつきものです。人の行動を規制するルール作り、何かのイベントの企画から終了までのプランニングなども全て「設計」。
何かモノやコトを作りこむ時に失敗を少なくするための手法のひとつがFMEAなんです。
とはいえ、今回も製造業を例にとって説明しますね(笑)
その他の業界のみなさんは、自分の会社だったら…と置き換えてみてください。
FMEAで導いた設計項目の信頼性数値を活用して得られるメリットを下の図のようにまとめてみました。
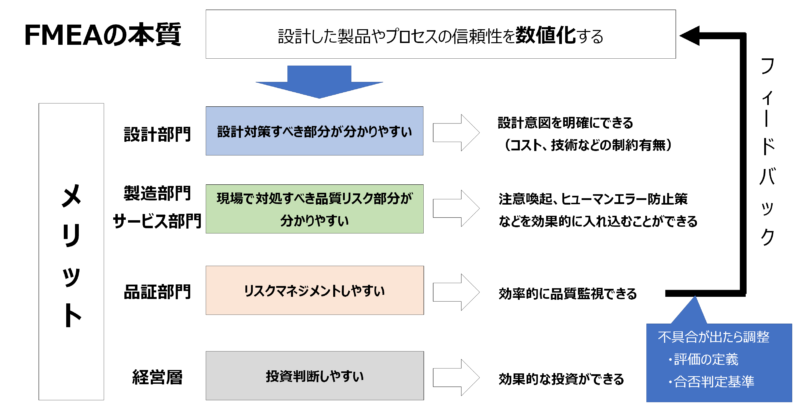
以降でもう少し細かく説明していきますね。
設計部門にもたらすFMEAのメリット
メリットの前に少しおさらいです。
ここでいう設計部門は製造業の量産工程設計を指していますが、これがプログラム設計プロセスだったり、サービス提供マニュアルだったりしてもいいわけです。
何かを作り出すためには、数々のステップ(工程=プロセス)を踏まなければいけません。そのステップにはどんなものがあるのか、細かく分けてその細分化された要素を意図をもって設計しているわけですよね。
ある工程にはいくつかの設計された作業があって、その作業を守らなかった・または守れなかった事象を故障モードとして列挙し、
・故障モードが後工程やユーザーにどのような影響(機能不具合や事故など)を与えるか
・故障モードの発生対策度合いはどの程度か
・故障モードが起きた時の検出度合いはどの程度か
という3つの観点で最適設計していくのが工程FMEAです。
※ちなみに製品の構造設計の場合は、部品と部品をつなぐインターフェース部に着目して行う場合が多いですね(例:はんだ付け、ネジ締め、圧入、溶接など)。
評価点の付け方はネット上をみても様々な定義の仕方がありますが、ここは業界や会社それぞれで決めていくべきところ。
評価ランクを細分化しすぎると評価に時間がかかったり、評価結果自体がリスクが高いのか低いのかが分かりにくくなるからです。そうなると長続きしません…。組織に適した尺度を作り上げましょう。
以下の記事で例と示している「家族と水族館に行く工程」のFMEAを行ったときの評価の付け方はこうです。
【日常生活でFMEA活用の具体的事例解説】家族で水族館にいく工程の信頼性を評価する【初心者向け】
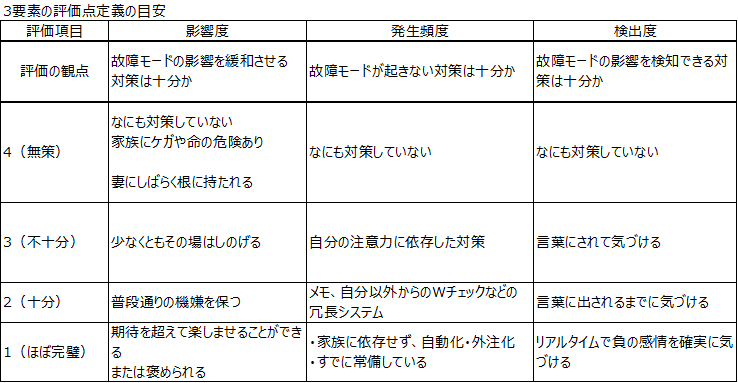
評価ランクはなるべくシンプルな分類が望ましいです。不完全でも実績を事実のまま残して、後工程で不具合が発生するのであれば、再発しないように定義を見直せばいいのです。
さて、ある製品の製造工程を設計したとしましょう。
この工程は2つの工程で構成され、それぞれの工程で5つの作業があり、それぞれの作業ごとに故障モードを列挙(全部で15の故障モード)し、影響度と発生対策度合い、検出対策度合いでリスクの総合評価を行いました。
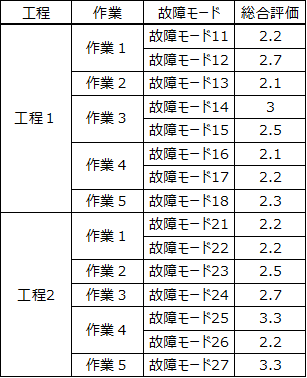
グラフにするとこうなります。
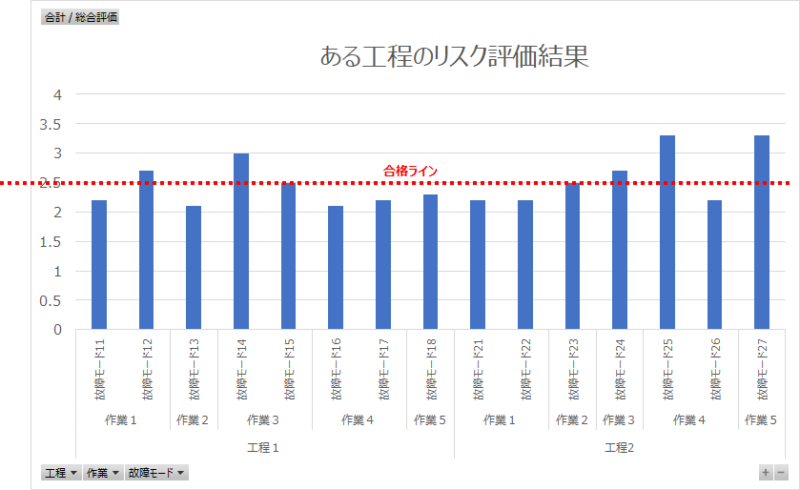
ここで総合評価2.5点以下を「合格ライン」としていますが、これは各組織内でこれまでの実績などを加味して決めるべきでしょう。今後の不具合発生状況や会社が投資できる限度なども考慮する必要があります。
もちろん設計者はなるべく評価点数(リスク)を低くしないといけませんが、点数が悪いからダメだという訳ではありません。コストや技術的な制約もありますからね…。
設計時にリスクが高いと意図しているということが分かればいいのです。
そうすれば、後工程である製造現場にリスクの高い工程を説明しやすくなり、あとは現場で不良が出ない対応をしてもらうよう引き継ぐことができます。
このように、設計者の設計意図と共にリスク度合いが可視化できるため、他の設計者や他部門が見ても設計の意図とリスクが把握しやすくなるというメリットがあるのです。
始めに少し手間をかけて可視化してあげると、現場に引き渡して問題が起きてから設計部門が引っ張り出されることも減っていくでしょう。
もちろん、この他にも若手育成の資料にできたり、FMEAを通して設計者自身のレベルアップにもつながたりという面もあることも想像できますよね。
製造・サービス部門にもたらすFMEAのメリット
設計された工程を実際に運用するのは製造・サービス部門になりますよね。
あらかじめリスクが可視化されているので、「どの工程」の「どの作業」がリスクが高いかが一目で分かるようになっているので、ポイントを突いて現場側で注意すべき箇所に対応することができます。
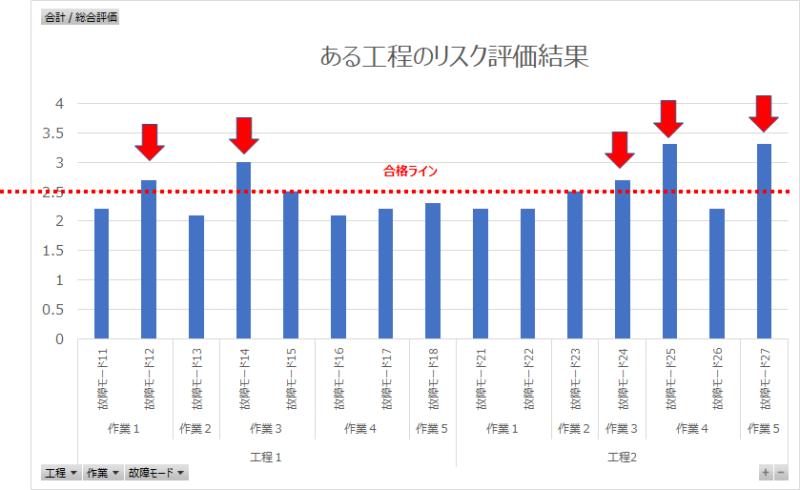
Wチェックを入れる、モノの置き方を変える、デジタル機器や治工具などを使って人に依存しないようにするなど、作業する人が意図せず設計通りの作業ができなくなるのを防ぐための仕込みを入れてあげればよいのです。
もちろん、設計時点でFMEAレビューに参加し、事前に製造側でリスクと思われる作業には何とか設計側で対処できないか議論するのがベストです。
物事がうまくいくか・いかないかは事前の段取りで8割決まるとも言われてますからね!
これで不良が出なくなって、対策書やらリカバリーでの余計な労力を減らすことができると思ったら利用しない手はないでしょう。
品質保証部門にもたらすFMEAのメリット
設計部門や製造・サービス部門の品質管理が問題ないかを監督する品質保証部門にも大きなメリットがあります。
技術的な知見がなくても、FMEA結果を見れば設計でのリスク度合いを把握することができます。
品証部門が不具合対応でお客様に使う労力が減ると思えば、是非FMEAレビューを設計部門と一緒に実施して事前に不具合の芽を摘み取りましょう。
過去の不具合データの蓄積があれば、設計部門が抽出できてないリスクをその場で対処させることもできますからね!
また、現場での運用が始まると「設計通り」、「現場のルール通り」の運用が行われているか品質パトロールで監視することもあると思います。
やみくもに全ての工程のすべての作業を確認するのは時間がかかりますし、多数の工程やラインがある場合は現実的ではありませんよね…。
FMEAの結果に基づいて「リスクの高い工程」の「リスクの高い作業」に絞って監視活動を行うことで効率的に品質を担保できます。
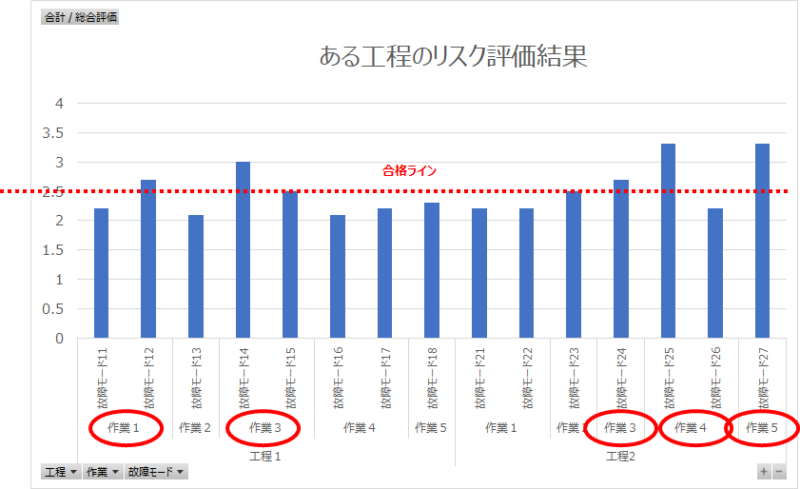
モノづくりにおいて、不良ゼロということは残念ながら現実的ではない場合も多々あります。
しかし、発生した不具合の原因を調査し、次の新たなFMEAに向けて評価点の定義や合格ラインの調整をすることで理屈に合った品質コントロールをすることができるのも大きなメリットと言えるでしょう。
ある程度長いスパンで全体のレベルを上げていく意識で臨むと良いと思います。
業種によっては人命に関わる製品やサービスを行っている組織もあると思います。
そのような業種では安全マージンをとって厳しめの評価定義と合格ラインを引くことで会社経営への大きなリスクを減らすことも考えなければいけません。
社会的責任の大きい組織においては、FMEAは必須と言ってもいいかもしれませんね。
経営層にもたらすFMEAのメリット
ここまでくれば、経営層にもメリットとなることは誰でも理解してもらえると思います。
上級管理職ともなると、今現在の現場のどこにどんなリスクがあるかなんて細かく把握している人は少ないんじゃないでしょうか?
まあそれが問題という訳ではないですが、現場や中間管理職の人たちからすると現場のことはある程度知っておいて欲しいというのはあると思います。
FMEAの結果だけでも目を通しておくとリスク箇所がパッと見て分かるので、不具合報告などを受けるときは事前にFMEA結果を確認することをオススメします。
もちろんFMEAレビューに参加し、設計・製造担当の声と総合的な評価結果によるユーザー影響を加味することで、的確な投資への判断材料とすることができます。
単発で「これに投資させてください!」と言われるよりも、必要性が分かりやすくなります。
さらに、レビューに参加することで現場でのコストや技術的な制約を把握することも経営層としては必要だと思うので、FMEAが社内に定着できるように先導するべき立場なのかもしれません。
さいごに
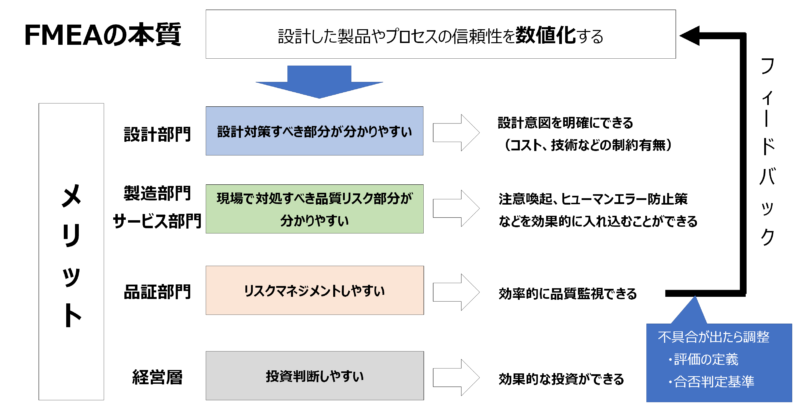
FMEAは細かくやればやる程時間がかかります。
時間かけた分だけ効果が出るかと言われると分かりません。
ですが、それが未然防止・予防というものじゃないでしょうか?
何かあった時にはもう遅い、莫大なロスが発生する…そんな事態にならないための予防です。
当然手間もかかるし、普段は「こんなことまでやる必要あるんだっけ?」と思うでしょう。
しかし、FMEAもウィルス感染防止のマスクや手洗い・うがいと同じことなのです。
実際にやってみるとメリットもたくさんあります。
目の前の労力を惜しむより、将来労力をかけなくて済むように未然防止活動にリソース投入できるといいですね~ということで今回の記事はおわりです。
おわり
コメント