筆者である僕は、製造業の品質保証部門で10年以上試行錯誤しながら品質向上のために働いています。
これまでの経験を通して最近特に感じることがあります。
それは、
製造やサービスの現場の品質は、現場の班長やリーダーなどの末端の管理者に大きく左右される
ということ。
このように聞けば、多くの方は「当たり前のことだろ!」と思うでしょう。
遅いか早いかは分かりませんが、40歳を超えてようやく僕もそう思えるようになりましたよ・・・
そこから一念発起した僕は、実際に複数の協力会社も含めた現場リーダークラスの意識調査のためにアンケートを行いました。
今回の記事は、
・現実の製造品質とリーダーの意識調査結果から読み取れること
・製造品質向上のため、現場の班長やリーダーをどのようにサポートしていけばよいのか
という点について述べてみたいと思います。
・僕の立場は情報通信機器製造の品質保証部
・協力会社の従業員含めれば1000人以上の規模
・アンケートは無記名回答(本音を引き出すため)
・調査対象は製造ラインの班長、リーダークラスのみで6社、計24名
まずは、アンケート結果と考察の前に、直近1年間の品質状況などを簡単に説明します。
調査対象組織のパフォーマンス概要
自社も含めた6社で情報通信機器を1年間製造した各組織のパフォーマンスを下図に示します。
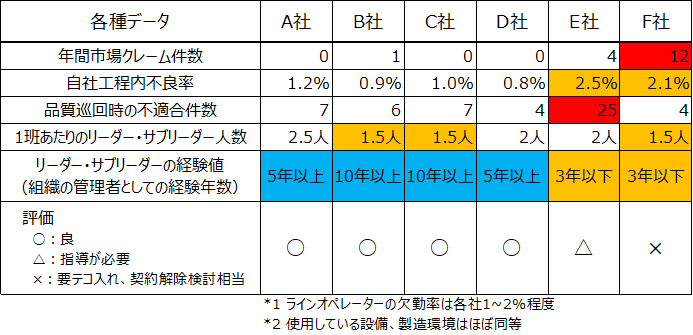
A,B,C,Dの4社は、お客様先で発生した重要障害による市場クレーム件数は極めて少なく、製造プロセス内での不良率も比較的悪くないレベル。比較的高めの評価を受けています。
E社は、市場クレームはやや多めで製造プロセス内での不良率が高く、さらに我ら品質保証部のQCパトロールにおける不適合件数がダントツに多い。低評価をせざるを得ないレベルです。
F社は、品質パトロールの不適合件数は少ない方だが、圧倒的に市場クレーム件数が多く、製造プロセス内での不良率も高いという状況。結果だけ見れば最優先でテコ入れするか、契約解除を検討すべきレベル。
注:パトロールでの指摘が少ないということは、ルールの目的を理解しないまま形だけはルールを守っている
というような状況です。
冒頭でも述べたように、「現場リーダーの日々の指導や管理が製造品質に関係するのではないか?」という観点で
・ラインあたりのリーダークラスの人員数
・そのリーダークラスのリーダー経験年数
を加えています。
上記のような結果から、以下のように考えました。
■市場クレームが少なく、工程内不良も少ない、そしてルールの順守意識も高いラインの特徴
・ラインリーダーの経験値が高い
・1ラインにリーダークラスの人員を多く配置
そして、逆に悪いパターンは以下。
■市場クレームが多く、工程内不良も多い、ルールの順守意識も低いラインの特徴
・ラインリーダーの経験値が低い
・1ラインあたりのリーダークラスの人員が少なめ
まあ、見たまんまの結果を書いてるだけですけどね。。。
つまり、ラインリーダーに経験値が高い人がいることが最も効果的で、さらに複数人いれば高いレベルの管理や指導、改善活動ができてパフォーマンスが高くなるるというもの。
当たり前っちゃあ当たり前ですが、このような観点でマジメに数字で比較したことがない人にとっては、改めて数字で見ると「やっぱりそうかー」という気持ちになりませんか?
じゃあ、パフォーマンスをあげるためにはどうしてあげるのがいいのかなぁ?
ということで、まずは実態を知るために実際に現場で働いているリーダーたちに意識調査してみました。
というのが、今回の意識調査に至った経緯です。
現場リーダーたちの意識調査結果
まずは、意識調査アンケートの全設問の内容です。
Q1. QCD(品質、お金、納期)の3つの要素の中であなたが最優先したいと思う要素は何ですか?
Q2. Q1に対して、現場の実態は何を最優先していると思いますか?
Q3. あなたは、上司からQCDの何を大切にするように指導されていますか?
Q4. あなたの上司は、あなたの仕事の問題や課題を解決するための助言をしてくれますか?
Q5. あなたは、管理している班やグループの問題や課題を改善する余裕を持てていますか?
Q6. あなたは、あなたが担当している班やグループをしっかり管理できていると思いますか?
Q1~Q2は、QCDについてリーダーの思いと現場の実態の乖離具合を図るためです。
※Q(Quality:品質)、C(Cost:お金)、D(Delivery:納期)
Q3~Q4は、リーダーとその上司のミスコミュニケーションの有無を確認。
Q5は、リーダーとしての業務を行う時間的な余裕の有無を確認。
Q6は、リーダーの自己評価を確認。
さて、意識調査の結果と考察です。
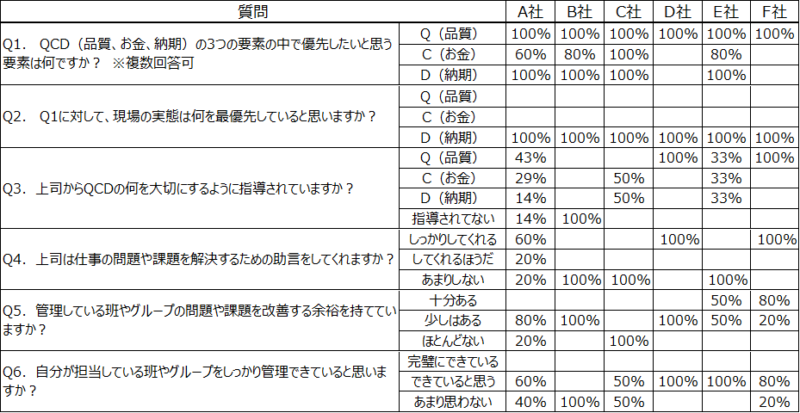
QCDの理想と実態の差

Q1. QCDの中であなたが最優先したいと思う要素は何ですか?(複数回答可)
多くの方が「QCD全て」、または「Q(品質第一)」という結果。
意外と「C(お金)」よりも「D(納期)」を優先しているリーダーが多いことから、現場は「品質」と「納期」のせめぎ合いであることが読み取れますね。
なお、当ブログでは「QCD全て」を優先することを良しと考えていません。
「全てが大切」という基準では重要な局面での判断基準が人任せになり、体調や感情でコロコロ変わる恐れがあるので組織の理念としては相応しくないという主張です。
しかし、理想として持つこと自体は全然悪いことではないので、ここでは問題としません。
日本特有の文化なのか、会社の文化なのかは分かりませんが、少なくともすべてのリーダーたちが品質を疎かにしたくないという心理はあると言っていいでしょう。
Q2.現場の実態は何を最優先していると思いますか?
Q1でリーダーの理想を聞いたうえで、現場の実態を確認します。
結果としては、
100%の人が「D(納期)」を優先しているのが実態
だと回答しています。
無記名とはいえ、「よくぞ本音を教えてくれてありがとう!」という気持ちです。
なぜなら、実際のところ現場は納期優先でやってる雰囲気見え見えですし、そうなるのも仕方ない状況であることは明白。
なのに周りの人間は、それを承知のうえで表面上は品質重視と言っているのです。
※注:今回の調査ケースの場合なので、すべての現場がそうではないと思います。
そんな環境、文化で効果的な品質改善ができるワケがないと考えます。
まずは実態をしっかりと自覚し、共有すること。
その第一歩を踏むことができる回答でした。
この結果によって、「理想と現実のギャップ(=問題)があること」を定性データとして表すことができました。
少なくとも僕は、リーダーたち個人のせいで品質が悪くなるなんて全く思っていません。
「リーダーとして現場を管理できる環境を作れない組織」のせいで品質が悪くなると思っています。
ヒアリングだけで終わらず、「意識」のような数字に表しにくいものを数値化していくことで、経営層へ実態を客観的に理解してもらうことが今回の調査の目的です。
例えば、ヒアリング結果だけで品証部から製造部門へ報告する場合に
「AリーダーとBリーダーにヒアリングした結果、現場の実態は品質よりも納期を優先しているようです。トップダウンで指導をお願いします。」
と伝えても
「本当にそうなの?」(と言いつつ、本当は実態を知っている)
「ふーん。分かった。是正させるわ。」
程度で終わることが多いこと。。。
言葉を変えて、
「あなたの部門の現場リーダーの○○%の人がこう思っています。指導や環境に問題や課題がありませんか?一緒に課題を解決していきましょう!」
と伝える方が、相手にとっても経営層にとっても説得力が上がる気がしませんか?
すみません・・・話を戻します。
ここまでの回答は、僕が予想していた通りの結果です。
全員が納期最優先の実態となっているにもかかわらず、各社のパフォーマンスが異なるということは、リーダーのスキルや経験、時間的余裕や上司からの指導などが関係しているのではないかと考えました。
現場リーダーと上司のコミュニケーションの実態確認
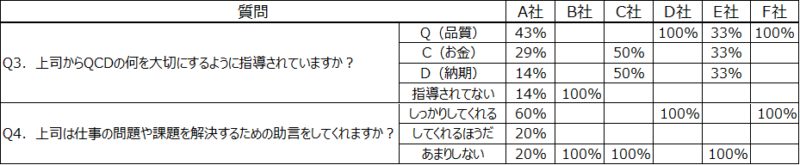
Q3:あなたは、上司からQCDの何を重視するように指導されていますか?
Q4. あなたの上司は、あなたの仕事の問題や課題を解決するためのアドバイスをしてくれますか?
品質第一を標ぼうする会社であれば、Q3は100%「Q(品質)」を重視するように指導を受けていると答えるはずです。
しかし、実態は各社バラバラといった結果。
A社の場合
A社の場合、品質重視と指導されている人が多いですが、お金や納期、または特に指導されていないと思っているリーダーがいるという事実があります。
リーダーの上に立つ人間たち(課長以上)からの指導方針が一貫していないという表れと言えるでしょう。
一方で、上司は問題解決、課題解決のためのアドバイスをしっかりしているようです。
比較的リーダー経験は低めの方が多いA社ですが、
それでも品質的なパフォーマンスが高いということは、「リーダーの経験値の高さ」と「1製造ラインあたりのリーダークラスの人数の多さ」に加えて「上司の手厚いサポート」が効いているという仮説を立てる根拠になり得ます。
B社の場合
B社の場合、特に指導されていないと答えたリーダーが100%。
B社の管理者は、事務的な対応に終始し、リーダーへの指導を怠っているということが言えます。
それでも高いパフォーマンスを維持できている理由は、リーダーが持っている現場管理能力の高さに他ならないでしょう。
過去の指導者によって鍛えられたのか、我流で学んでいったのかは分かりませんが、僕もB社のリーダーはレベルが高いと感じています。
「1ラインあたりのリーダー数」は少ないですが、リーダーの経験値と能力の高さでなんとか維持しているという状況が想像できます。
しかし、なにも指導を受けていない、アドバイスもくれないと思っているリーダーは不満を溜め、上司との信頼関係が薄れていきます。
将来的には、リーダーたちはB社を離れてしまうことも考える必要があるでしょう。
C社の場合
C社の場合、お金、または納期を重要視するように指導を受けていると思っている人が100%。
管理者がいかに上っ面だけ品質第一と言っているかがよく分かります。
お金、納期を重視することは間違いではありません。
問題なのは、品質第一と公に発信しながら実際は異なる指導を行っていることです。
さらに、リーダー達は効果的なアドバイスをもらっていると感じていません。
B社同様、1ラインあたりの人数も比較的少ないのに高いパフォーマンスを維持できている理由は、リーダーの経験値の高さによるものでしょう。
上司に対する不満を溜めているのもB社と同様と考えられます。
D社の場合
D社の場合は、品質に関しては理想的な状態と言えます。
リーダーとその上司のコミュニケーションも良いようで、品質に関してはあまりこちらから言うことはありません。
A社同様ですが、D社のような組織だと取引先は安心感が持てますよね。
E社の場合
E社の場合、QCDの方針が一貫していません。
なおかつ、上司から満足いくアドバイスをもらえていないと感じています。
リーダーの経験が浅いうえに、上司とのコミュニケーションが不足していることが低パフォーマンスを招くことになっていると考えられます。
特に、我々の品質巡回時で複数回指導しているにも関わらず不適合を繰り返すということは、リーダーが現場を管理できるレベルにないということ。
そして、その上司も見本、手本となれる存在ではないということが伺えます。
実績としては市場クレーム件数は比較的少なく見えていますが、いつ爆発してもおかしくないリスクを常に背負っている状態と考えます。
F社の場合
F社の場合、QCDの指導は一貫しているようです。
上司からのアドバイスも手厚いと感じているようで、上司-部下間のコミュニケーションは悪くないように見えます。
しかし、品質パフォーマンスが低いのはなぜなのか?
リーダーの経験が浅く、ライン当たりのリーダー人数が少ないということもあると思いますが、上司とリーダーで意識が合っているようで合っていない=上司の指導を正しく理解していないということも考えるべきでしょう。
上司が指導したことを分かったようで分かってない
そして意思疎通できていないことをお互い自覚していない
ミスをミスと認識していない
わりと組織として致命的な状態かもしれません・・・。
円滑なコミュニケーションができているのはいいですが、それだけではダメ。
ある程度のレベルを備えた人材も必要だということが改めて分かりました。
もはや文化が異なるレベルと考えて、手取り足取り指導するよりもテクノロジーのチカラを借りた方がいいのかもしれませんが、特定の一社のみに莫大な投資をするのは最善の策とは言えません。
現場リーダーの時間的余裕と自己評価の確認

C社を除き多くの協力会社では、リーダーとして問題や課題を改善するための余裕を多少なりとも確保できているようです。
C社のリーダーは余裕がほとんどない状況のようです。
前述のように、上司の指導も一貫せず、効果的なコミュニケーションも取れていない状況でも高いパフォーマンスを残せているということは、リーダーがプレーイングマネージャー的に現場に入り込んでいることが考えられます。
それはそれで今はいいですが、人員に余裕もない、時間的な余裕もない状況で何年も継続できるかと思うと疑問符が付きます。
将来の発展のため、少し余裕を持たせてやってくれ・・・というのが本音です。
E社、F社は比較的時間的余裕があるのに低パフォーマンスとなっているのは、確保できた余裕をうまく使いこなせていないからと思われます。
なのに、自己評価では管理できていると思っている・・・。
リーダー自体の品質管理レベル、もしくは上司の指導能力が低いことが原因でしょう。
B社のリーダーは、上司から十分な指導や評価を受けられず、管理ができてないと自己評価していることから、自己肯定感がかなり低い状態と言えます。モチベーションを上げるための施策が急務です。
なお、各社リーダー自身が管理している組織の「管理できている理由」、「管理できていない理由」を複数回答可で調査しています。
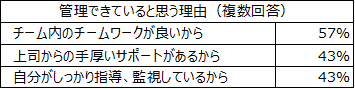
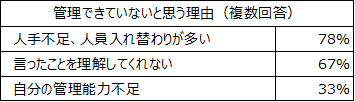
現場では、人員(数)とリーダークラスと作業者の人材(能力)が不足と感じているリーダーが多く、それでも管理できていると感じているリーダーは、ほぼ半数がチームワークと上司のサポートが手厚いと感じている。
つまり、能力のある人材確保と円滑なコミュニケーションが課題であることを改めて感じさせる結果となりました。
組織のパフォーマンス向上のためにどうするべきか
A~D社については、それぞれ高いパフォーマンスを示しているのである程度手放しでいいでしょう。
意識調査の結果、内部の事情はそれぞれの組織で異なることが分かります。
ある程度自律改善が望めそうな組織と判断している
我々が組織個別の事情に入り込むほどではないパフォーマンスを示している
ということから、今回の調査結果を各社経営層へフィードバックし、組織内の改善を促すにとどめておくのが良いでしょう。
あまり他部門や他社が深く入り込み過ぎると、自分たち自身で考えて、よりパフォーマンスを高めていこうという意識が薄れていく可能性があるからです。
自分たちでできることは、自分たちでやってもらう
彼らの成長のため、管理の手間を省いていくために、どんどん仕事を任せていきたいという考えがあります。
しかし、E社、F社については看過できない低パフォーマンスであるため早急なテコ入れが必要です。
とはいえ、リーダーのレベルアップや追加人員確保はすぐにできるものではありません。
まずは、リーダーの「さらに上の管理職」がしっかり現実を認識し、リーダーとのコミュニケーションの質を上げることが先決。
具体的な改善活動が行われているかどうかを、取引先として活動に入り込んで監視しながら進捗確認していくしかないでしょう。
1度や2度の教育や指導でどうにかなるものではありません。
長い期間をかけて育てていくつもりで、一緒に問題解決、課題解決して成功体験を増やしてあげる必要があります。
そんな手間ヒマかけたくないということであれば、取引先を変えることも考えるべきです。
ただ、E社の場合はトップダウンで
「ルールを破ってまで生産性を上げる必要はない」
と、ビシッと宣言してもらうだけで解決する可能性があります。
納期やコストの制約が緩和されると、ルールを守る意識が高まり、かつ生産性を高めるために非効率な現行ルールを見直すキッカケにもなるでしょう 。
そして結果的にQCDすべてが高いレベルになっていくと考えます。
手放しにできる自律した協力会社は、比較的コストが高めです。
このコストをどう見るか。
こちらの管理に手間ヒマ必要ない分、その時間を有効に活用できると考えると逆にリーズナブルなのかもしれません。
目に見えやすい取引上の金額だけでなく、組織の管理のためのコストも考えてみると選択肢が増えます。
今回の例では、主に協力会社に関する内容となっていますが、自社内のみの組織においても言えることです。
同じ社内の他部門を一つの協力会社であると考えれば同じこと。
社内の異動による人の入れ替えによってもパフォーマンスを変えることは可能。
しっかり管理されてきた組織は、リーダー以下の従業員もそれなりに規律正しく動ける習慣が身に付いています。
そんな組織を作り上げた優秀なリーダーを、テコ入れした組織に送り込むという提案もアリです。
今回調査を行った全体的な感想ですが、品質のパフォーマンス向上のために以下の2点を改めて検討する必要があると思いました。
①適切なコストを負担して人材を確保し、教育・指導を密に行っていく
②人への依存を減らすためにテクノロジー(機械化、電子化)を推し進める
どちらも重要で、どちらも手間とお金がかかる。
そして、どちらも現代の多くの組織にとって当然のように必要な活動。
どちらを優先するのかは経営者の判断次第ですが、少なくとも上記2点の観点で現時点できることをしっかり前に進めていくしかないと考えるに至りました。
さいごに
僕の考えは、
「管理職の理想」と「現場の現実」のギャップを埋めてパフォーマンスを維持しているのは、末端のリーダー達とそのリーダーによって管理されている作業者さん達の頑張りによるものです。
今回の記事を最後まで読んでいただき、共感していただいた読者ならば、何とかしてリーダーの頑張りに報い、評価や環境改善をしなきゃいけないと思っているのではないでしょうか?
ただ、現場を無視した一方的なサポートは、かえって現場を苦しめる可能性があることを忘れないでいただきたいのです。
あなたの思いと相手の思いは異なっていると考えましょう。
パッと見ただけで、ちょっと話しただけで他人の心の内側を把握することは不可能です。
そこを乗り越えて各組織の現場の実態にあわせたサポートをすれば、お互いハッピーになることができる。
組織の品質パフォーマンスを上げたいなら、まずはやってみませんか?
働く人の意識調査を。
①『新入社員でも本質が分かる!頼りになる製造業の品質保証部の在り方』
当ブログの要点をまとめ、新たに解説を加えた1冊。
新入社員でも品質保証の仕事の本質をつかみやすくなり、役割を明確にできます。
役割が明確になれば、主体的に動ける人材になれる!
※ご好評につき、期間限定のセール中! 390円→290円 この機会に是非。
【読者の感想】
興味深く拝読させて頂きました。
食品メーカー 品質保証部門長さま
とてもわかりやすくまとめられており、品質保証のそもそも論から整理したいと考えている我々には、まさにピッタリの内容だと感じました。
品質保証部門の方はもちろん、組織の品質意識を上げたい方が「どう考え、どう動くべきか」を導く1冊ですので、無料部分だけでも見てみてください。
期間限定セール中!
②【おすすめ品質教育手法】新入社員からベテラン使える「FMEA思考訓練」
筆者が実践してきた、新入社員~ベテランまで品質意識向上が図れる教育方法を解説します。
リスクを数値化する行為から多くの学びがある!
※こちらもご好評感謝の期間限定セール中! 200円→150円
期間限定セール中!
おわり
コメント